Powder Feeder for Cold Spray Additive Manufacturing
Applying a novel centrifugal concept to consistently feed <100 micron powder
I've been responsible for the design and fabrication of the centrifugal concept. Other team members have been responsible for developing other concepts, system controls, and the test stand.
End of Semester Summary Presentation
The presentation below is a summary of the whole project. More in depth details and discussion about the centrifugal concept is available below.
What is Cold Spray?
Cold spray is an additive manufacturing method that creates 3d structures using powders injected into a supersonic gas stream. One of cold spray's greatest problems has been the inability to consistently meter powder and drop the powder into the gas stream especially as the process begins using particles below 100 microns.
This project tackles the problem of consistently feeding and metering powder into the supersonic gas stream for a cold spray system at a Northeastern affiliated lab. It's analogous to the extruder in a FFF/FDM printer.
Powder Feeding
Powder feeding has been a persistent problem for centuries whose physics are still not entirely understood. There are a multitude of papers studying the consistent flow of particles such as sand and grain through a silo along with plenty of empirical data to back up theories. The data does not, however, include any relevant information about particles smaller than 100 microns.
In general, the smaller the particles are, the greater the effect of Van der Waal forces compared to gravity which leads to the particles easily "caking" (you might have experienced this with flour in the kitchen). In addition to this, we need to feed a variety of powders including ceramics, steels, aluminum, copper, and polymers which requires a generalized solution that can overcome caking, feed powders of varying diameters, and be wear resistant enough to withstand the ceramic powders.
Early Concept Generation
Our brief was short but anything but simple: "Feed powder of any material and any size in a consistent, repeatable manner, with a minimal number of consumable parts."
I've had enough experience waterproofing and making things airtight to find the thought of seals non-appealing...especially when I'm trying to seal <100 micron ceramic powder. The idea for the spinning funnel as a means of controlling powder came from my work on the coffee grinder project when I tried to integrate too many functions into the same part. These two projects were actually developed simultaneously in the summer!
Captions are listed in each photo for extra detail.
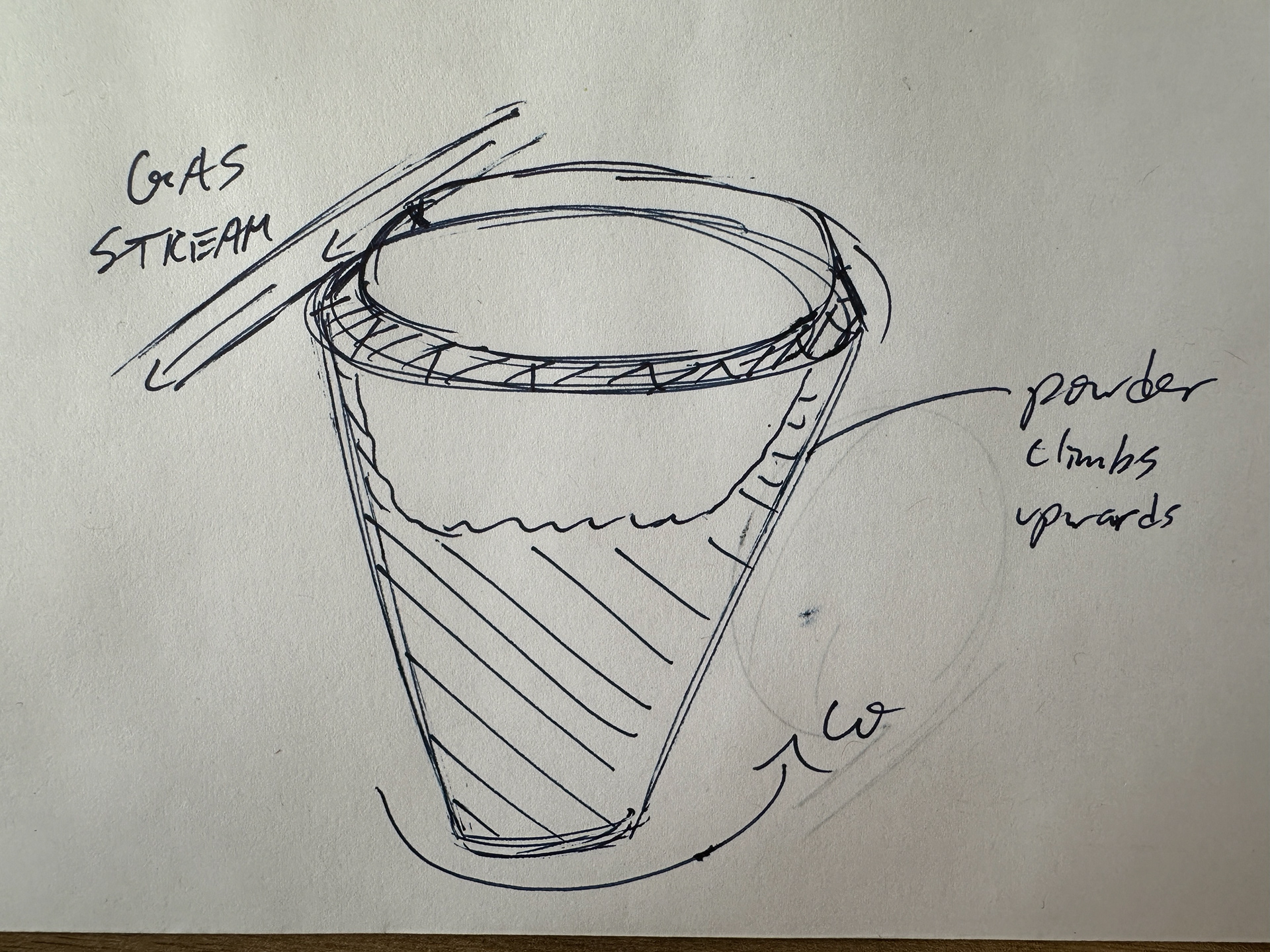
Early bowl concept that uses a high speed gas stream to carry powder that is drawn up the walls of the bowl.
Silo fed bowl concept that uses a shallow dish to fling powder down into a gas stream while using the rotation of the bowl to also drive an agitator in the silo through a gear reduction
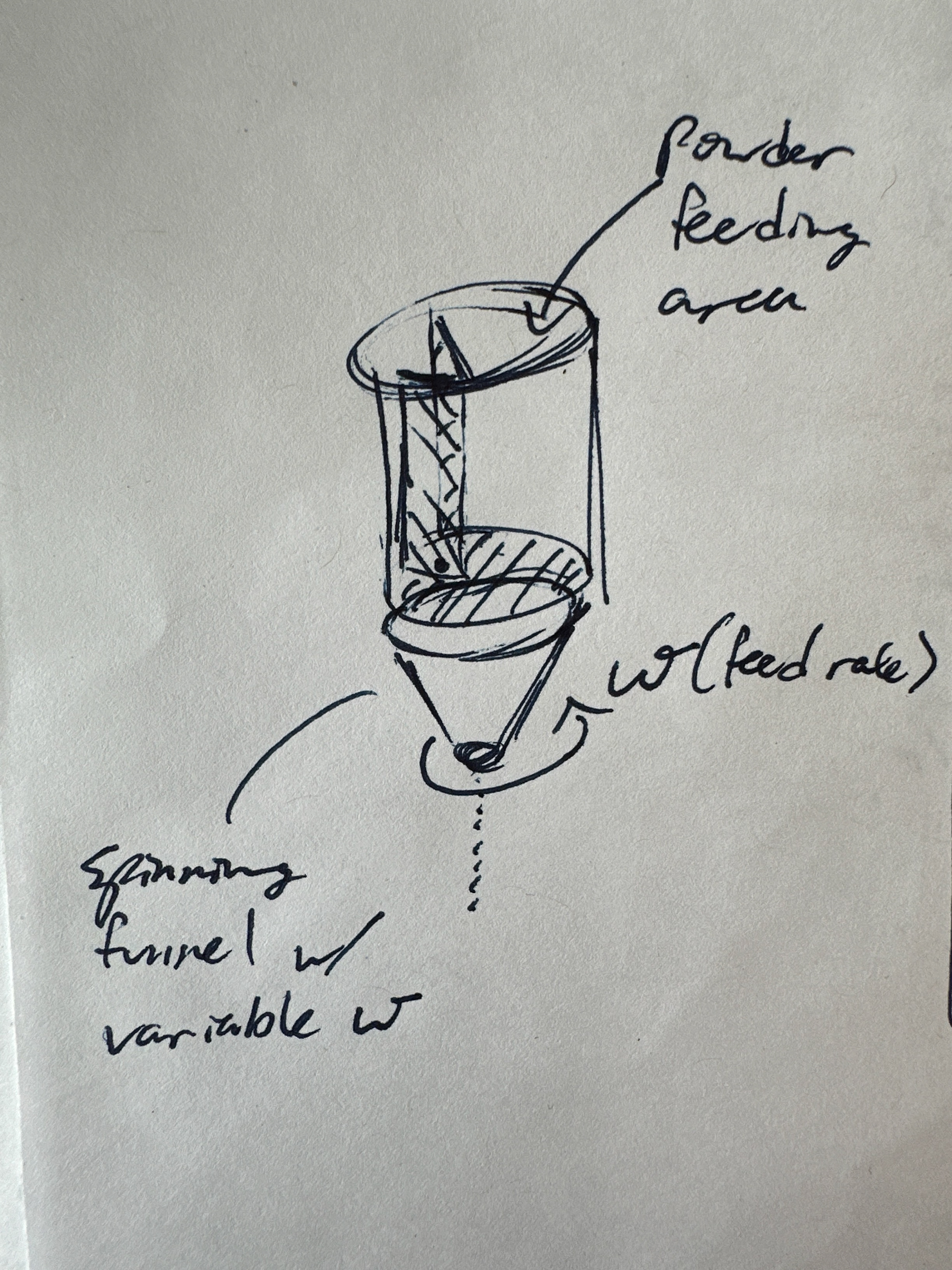
An early two stage rotating funnel concept that used a divider to control powder flow into a rotating funnel. The funnel would then both agitate and meter the powder for feeding.
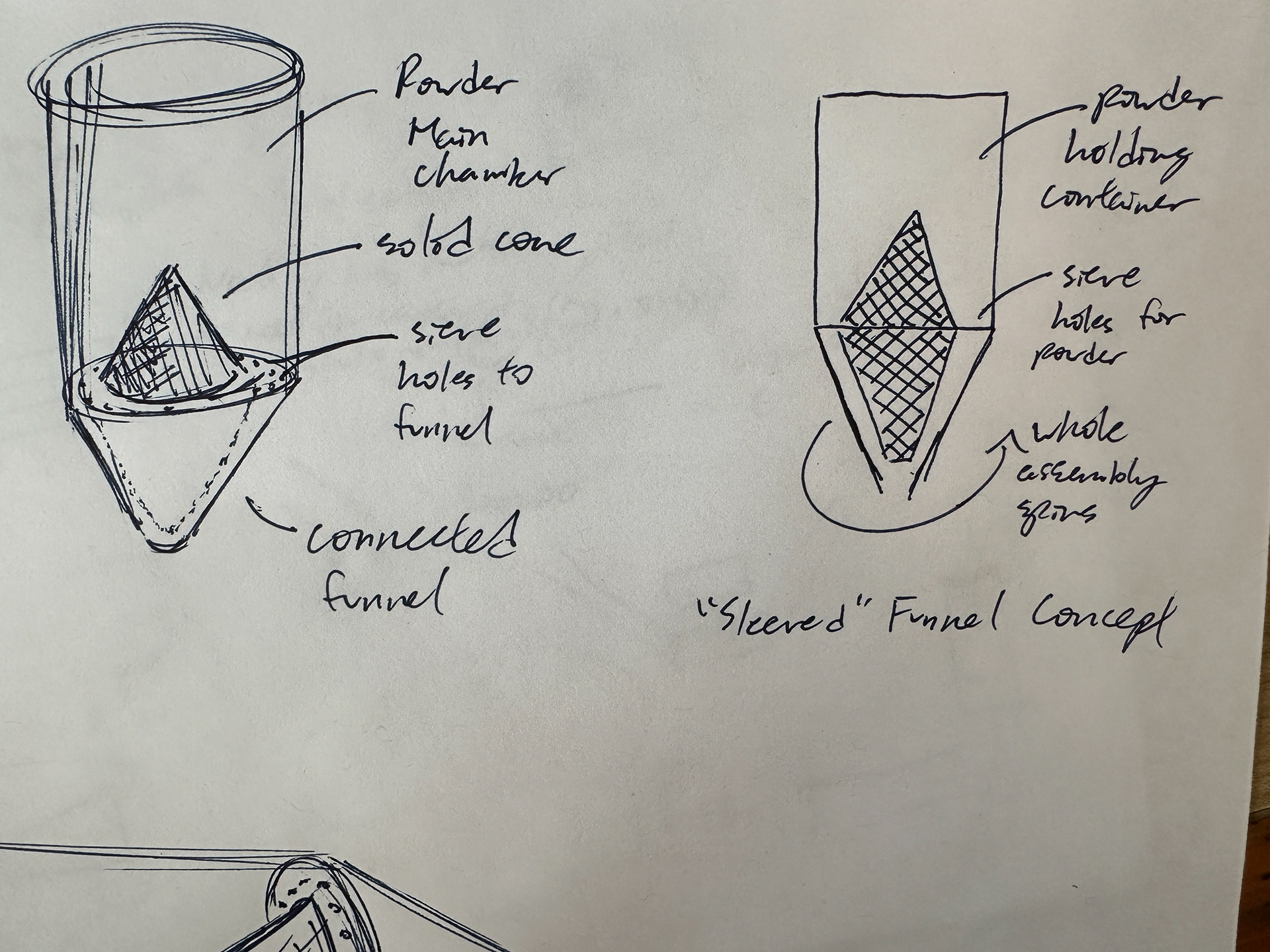
Annotated centrifugal cone feeder with section view
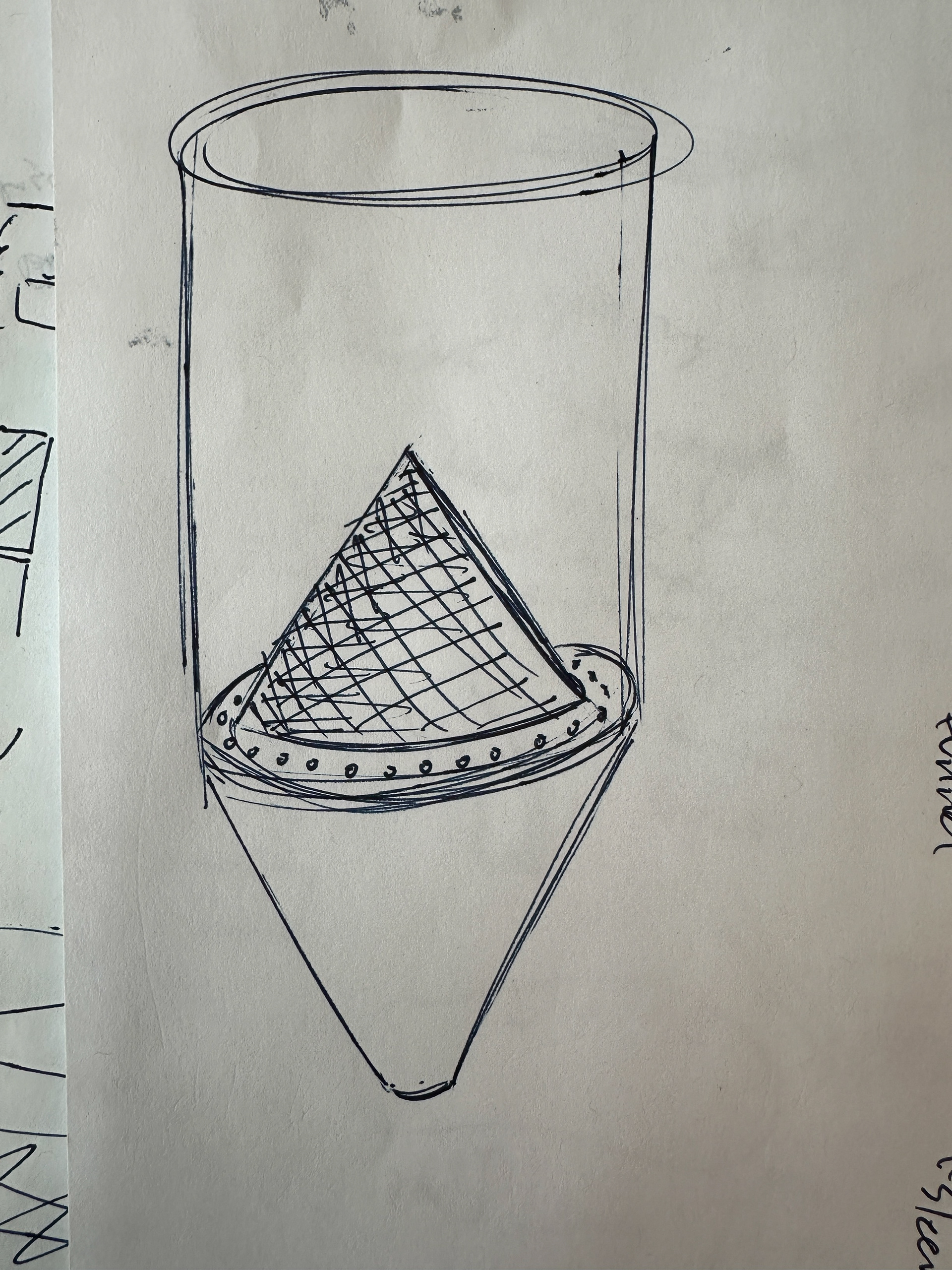
Refined 3d drawing of the centrifugal cone feeder
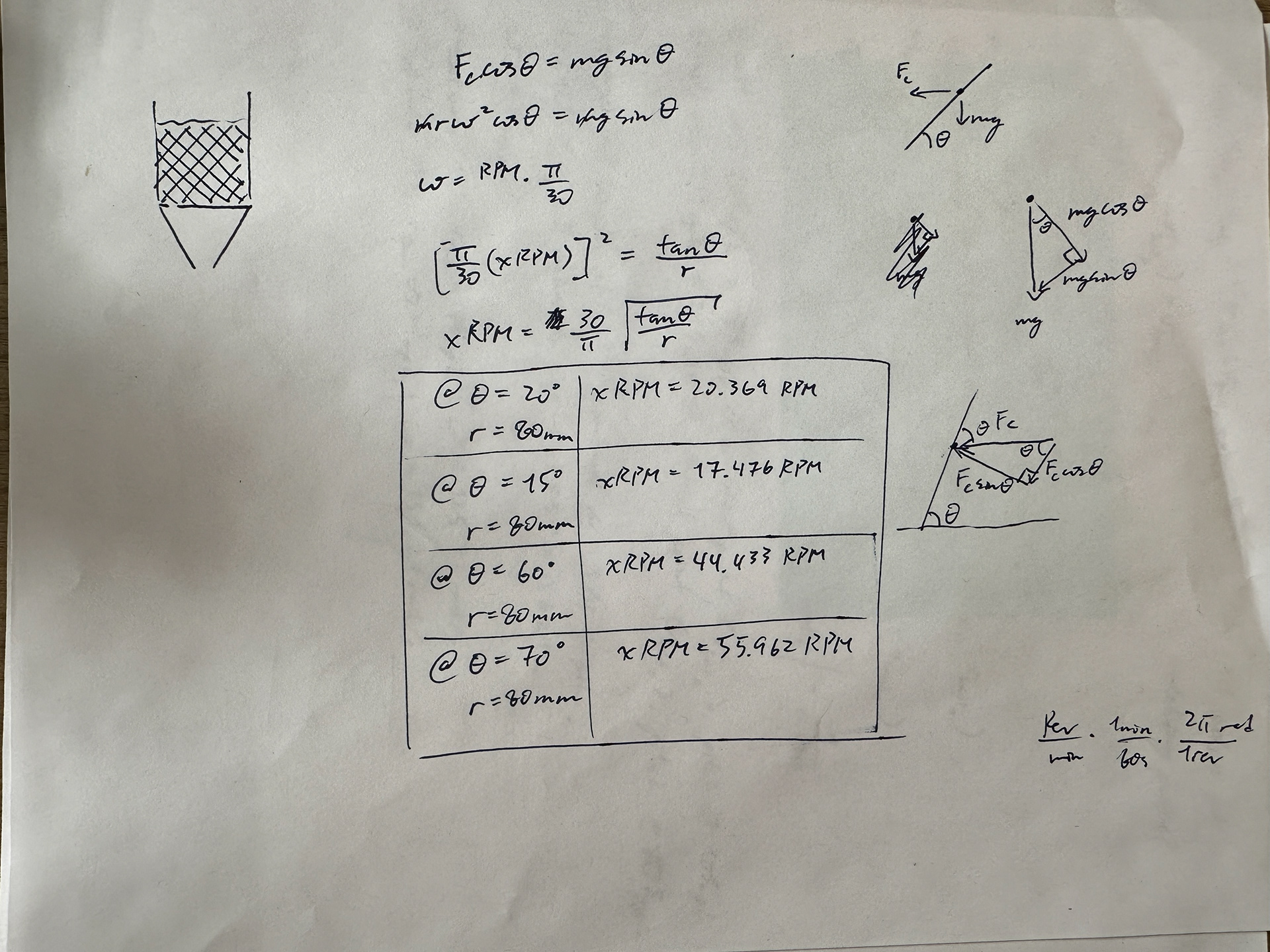
Preliminary calculations to ballpark rotational velocities and ensure concept was even feasible without complications in powder flowability.
Mathematical Analysis
If this concept has a chance of working, the centripetal forces need to overpower the assorted small particle forces (hydrostatic, Van der Waal, electrostatic). To test this, the geometry is generated purely based on the assumption that centripetal acceleration and gravity are the only meaningful forces in keeping the particle stuck to the wall. Any friction between the particle and the wall is a bonus.
Using the diagram on the left, we can find that it's possible to find an angle at a given radius and angular velocity that makes the sum of forces in x equal to zero. One problem though! The funnel's radius is constantly changing and the entire funnel can only rotate at a single angular velocity.
The definition of a derivative comes in handy here which allows for us to solve for the rest of the geometry using a set radius and angle. I've conveniently used this set radius and angle as the radius and tangent angle of the funnel where the powder exits. A little bit of rearrangement and the theoretical angular velocity necessary for "stability" can also be found.
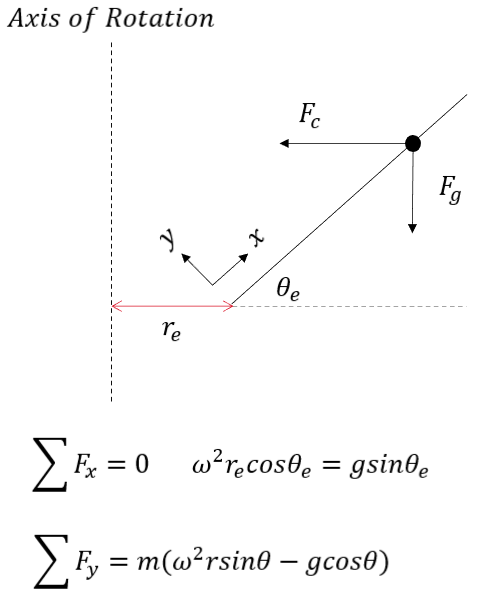
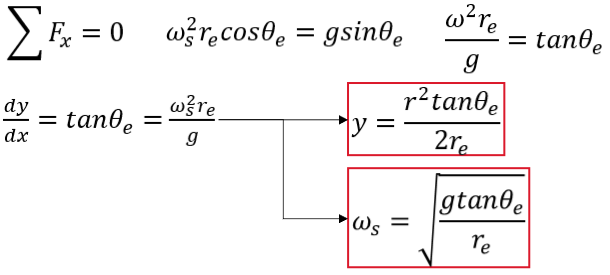
Design 1
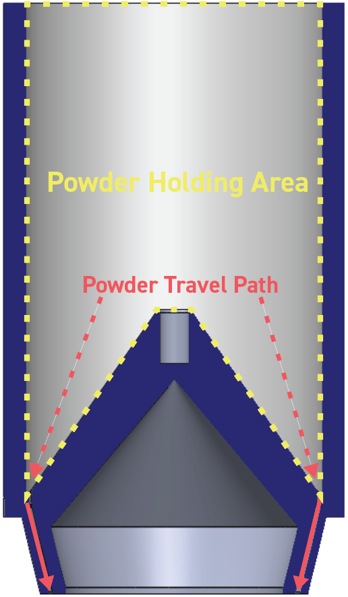
This design uses a single body that acts as both powder containment silo, agitation, and feed control with no moving seals. This design eliminates all wear components and making it feasible to print frequently with highly abrasive ceramic powders. Powder flow is entirely controlled by the rotation of the assembly.
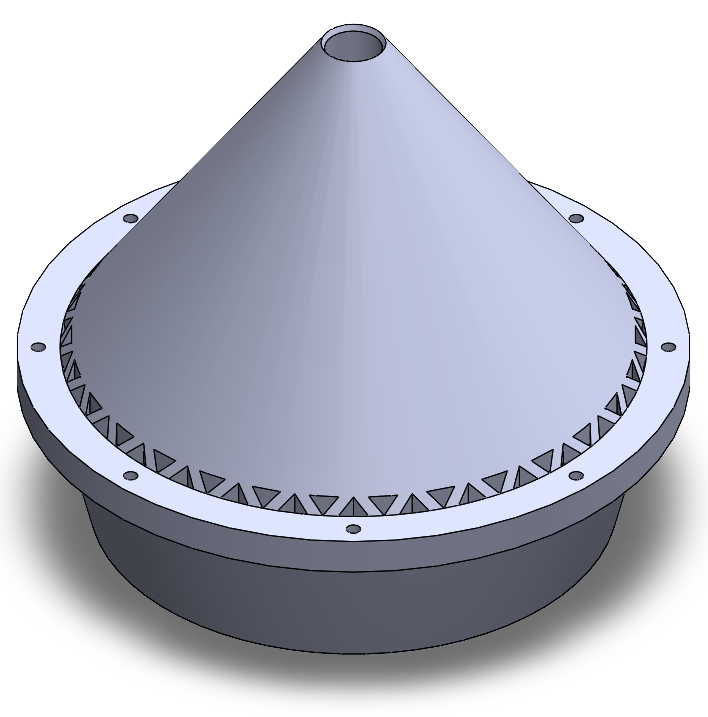
Closeup of funnel and its latticed sieve that feeds into the funnel
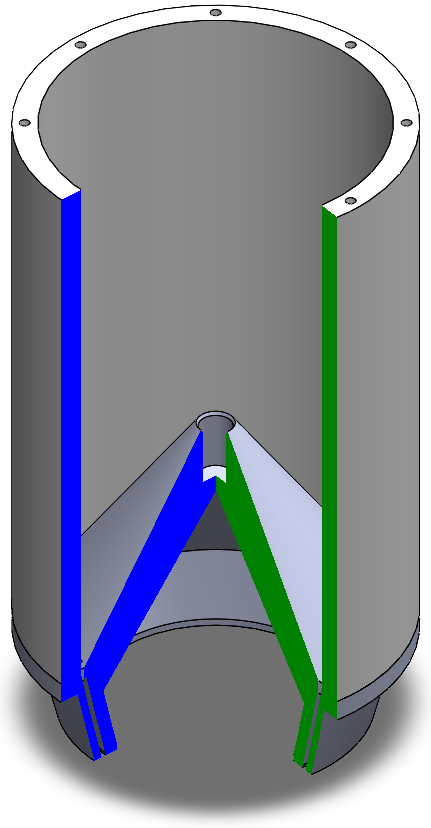
Section view of cone with drum as "one piece."
Design 2
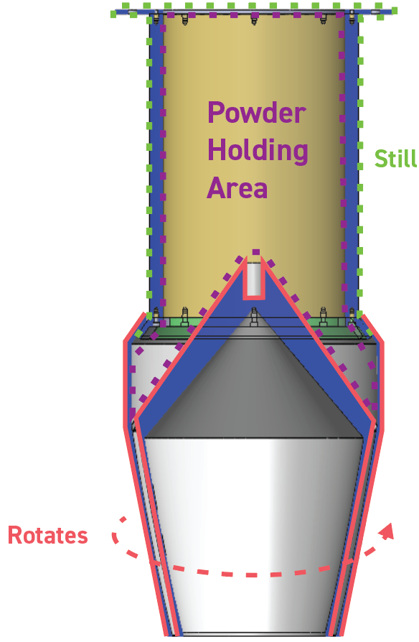
An alternative design, this system still uses the centrifugal funnel to control the flow of powder however the cone now spins independently from the silo. This increases the ability of the cone to agitate the powder, further agitate the powder column, and increase the predictability of the powder feeder.
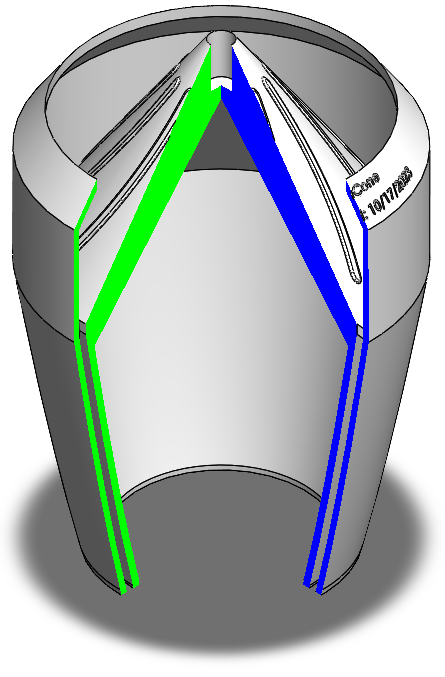
Cross section view of Design 2
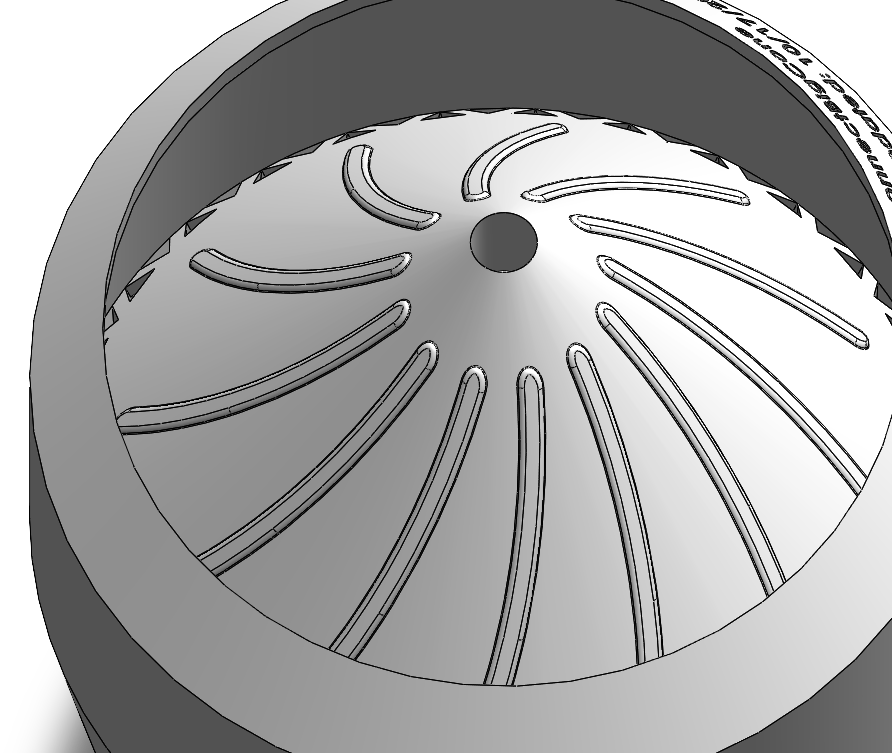
Bumps have been added to the top of the interior cone to increase agitation and feed powder towards the latticed "sieve." Heavy inspiration drawn from my Hario V60 coffee brewer!
Test Stand
Early testing with a mix of scrap powder that is 90% aluminum, we have proof that the concept is viable. Further tuning and testing is necessary to fully understand the effects of friction between the powder layers and between the powder and the walls, however the concept is proven to enable powder to stick to the walls without caking. This initial test has proven that friction is a significant factor in feeding.
Since this testing focused on proving the viability of the concept, the volume of the powder used and the scale of the prototype are much larger than what would be desired in actual implementation to allow for ease of manufacturing. Further tests will use a smaller funnel design that is closer to what would actually be desired in addition to measuring the feed rate by grams per second.
Data
Design 1 is an existing design from the manufacturer that relies on a rotating seal while Design 2 is the centrifugal design that has been discussed so far. Design 1 is touched up on in the presentation at the top of the page with some visuals if you are curious.
Overall, the centrifugal design was able to hold a feed rate that had 3.5x less deviation compared to the smooth metering mechanism though the centrifugal design proved to not be material agnostic. The nickel and copper fed at significantly differing rates despite the same angular velocities being the same for "high" and "low" feed rates. The significance of friction, as opposed to other small particle forces, could be confirmed by testing with a couple of other powders such as aluminum, ceramics, and plastics.
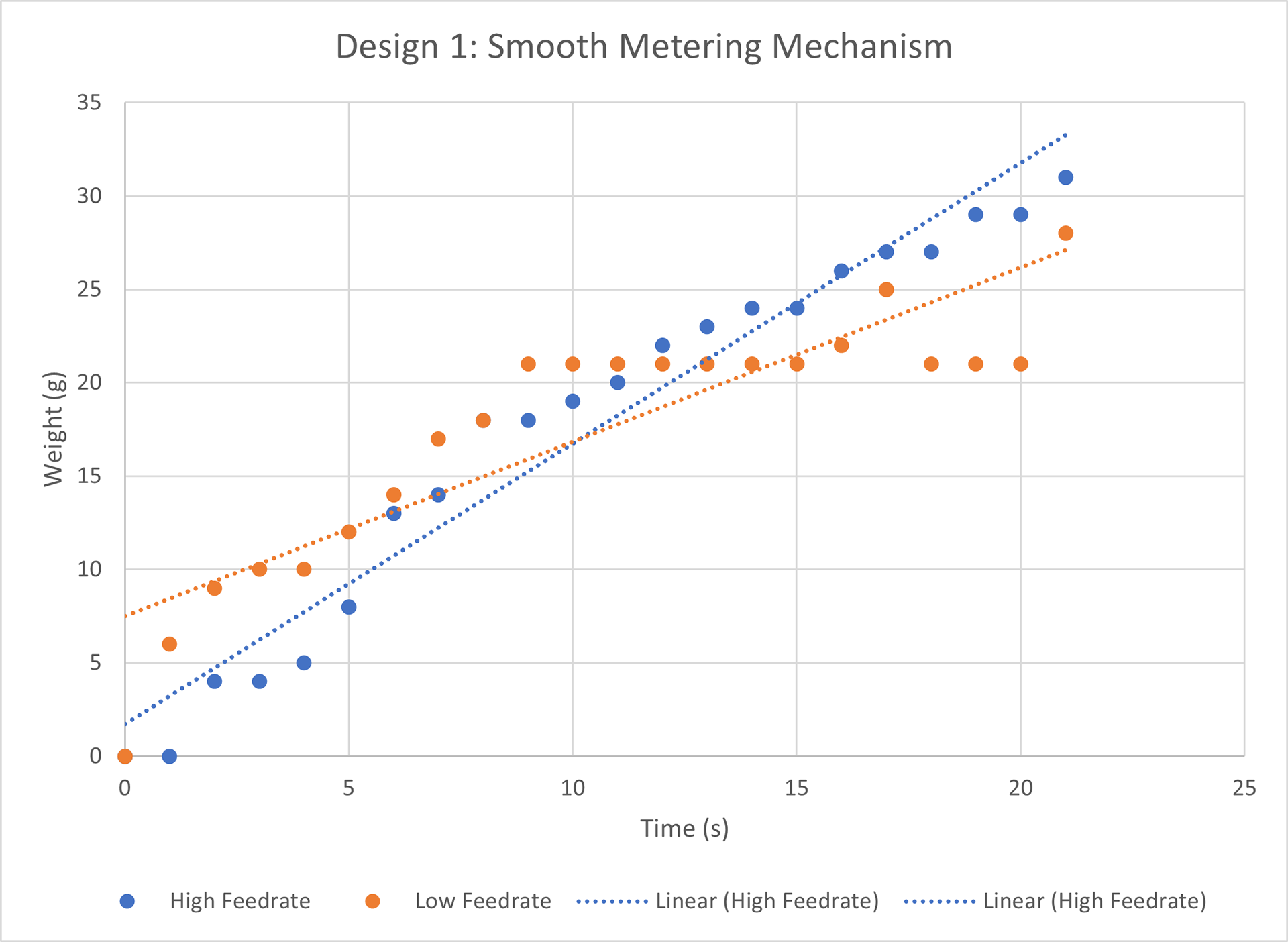
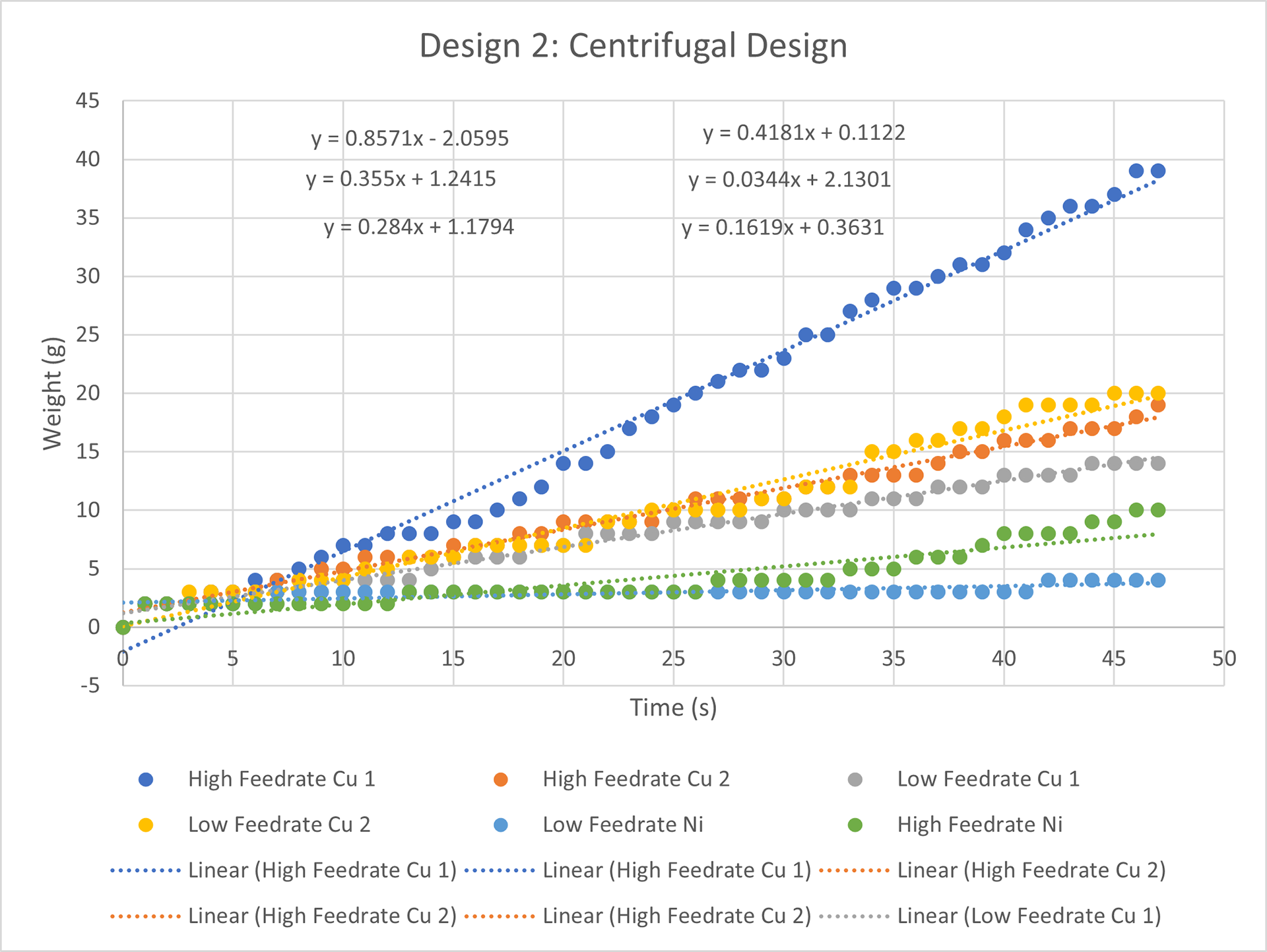
Results
Though the system has a narrow range of angular velocities that allow feeding and is not material agnostic, there is promise in its viability as a wear resistant, fine powder feeder that now only needs to compensate for the coefficient of friction of powders. By testing the feed rate of the powder at various angular velocities in a pre-print routine, there is a serious possibility of being able to solve for the coefficient of friction dynamically (before each print) for implementation in cold spray systems.