Espresso Grinder + Integrated Tamper
ME4550 (Mechanical Design Analysis) Class Project
Is it possible to integrate a flat burr grinder into an espresso tamper while still keeping the machine small enough for home use?
I lead the project and was responsible for the external ID, all mechanical design, and all renderings. Ultimately most of my attention was directed to the grind + tamp subassembly due to its unique, spring loaded design.
Problem Identification
Espresso can be a surprisingly messy experience, especially in an office filled with high energy people. Coffee grounds are often spilled en route from the grinder to the tamping station. The solution so far? Put a dark cloth near the spill zone to hide the spilled grounds.
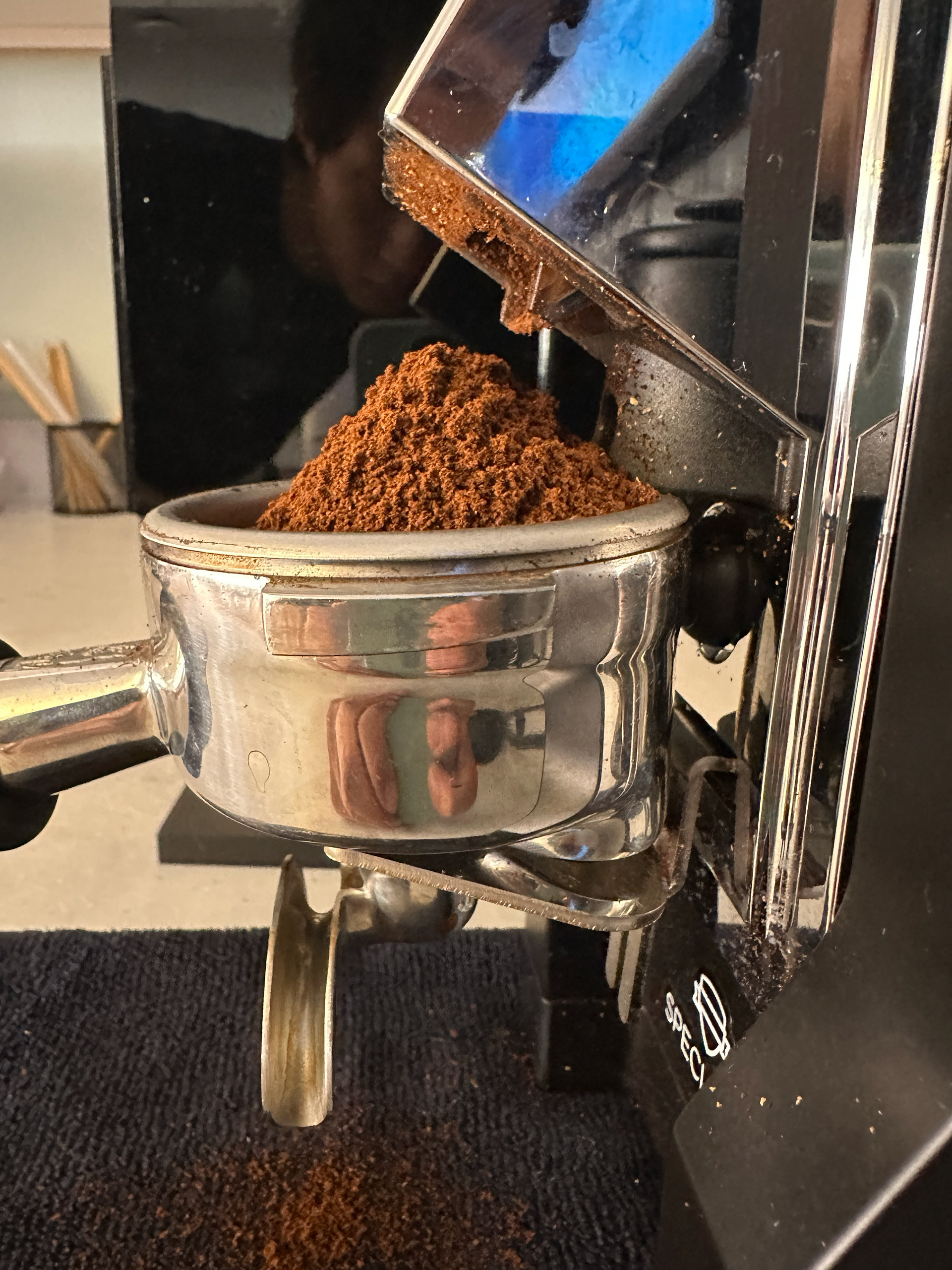
Grounds are deposited in a pile from the grinder

There's a tendency for grounds to electrostatically stick to things!
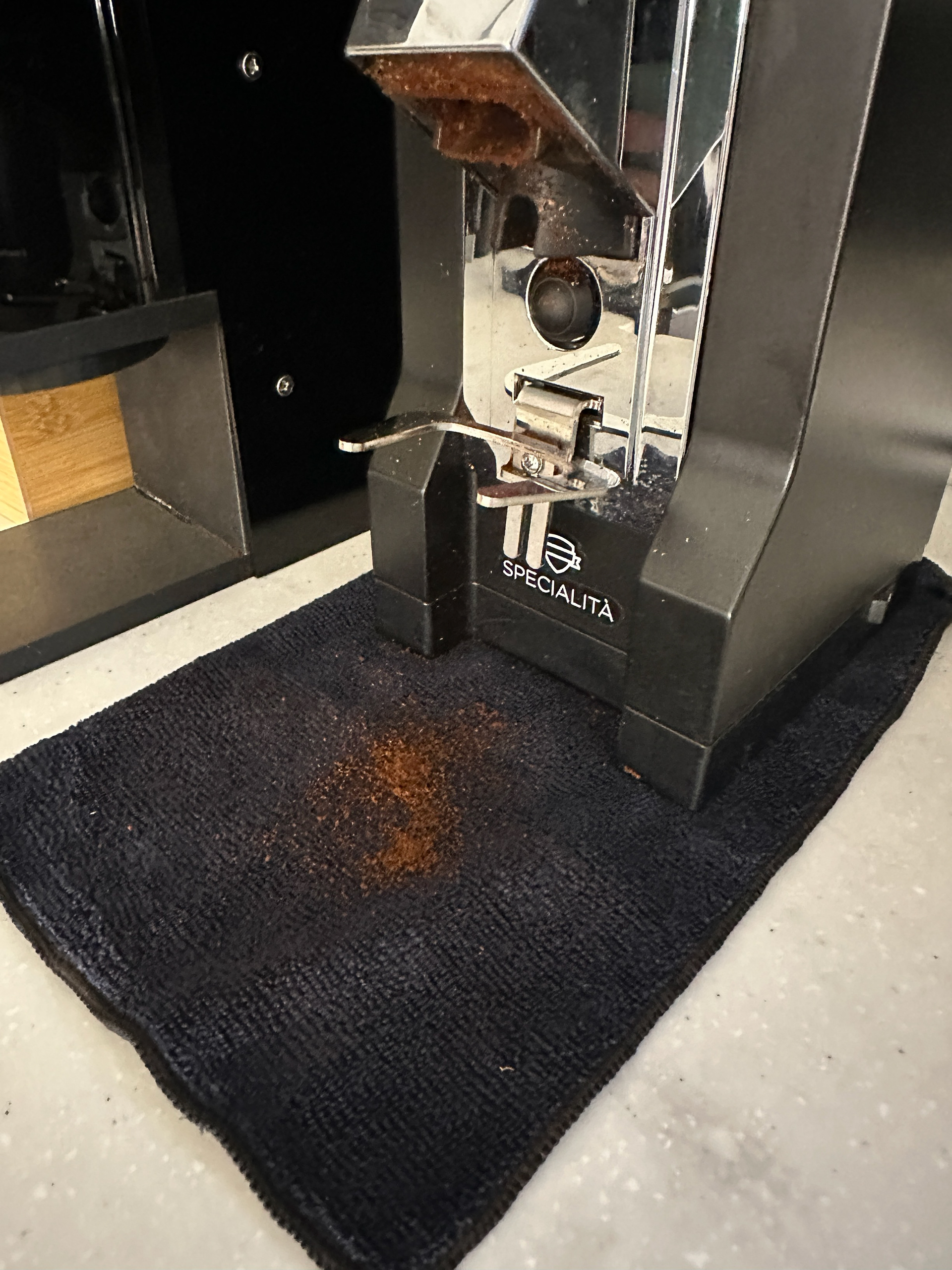
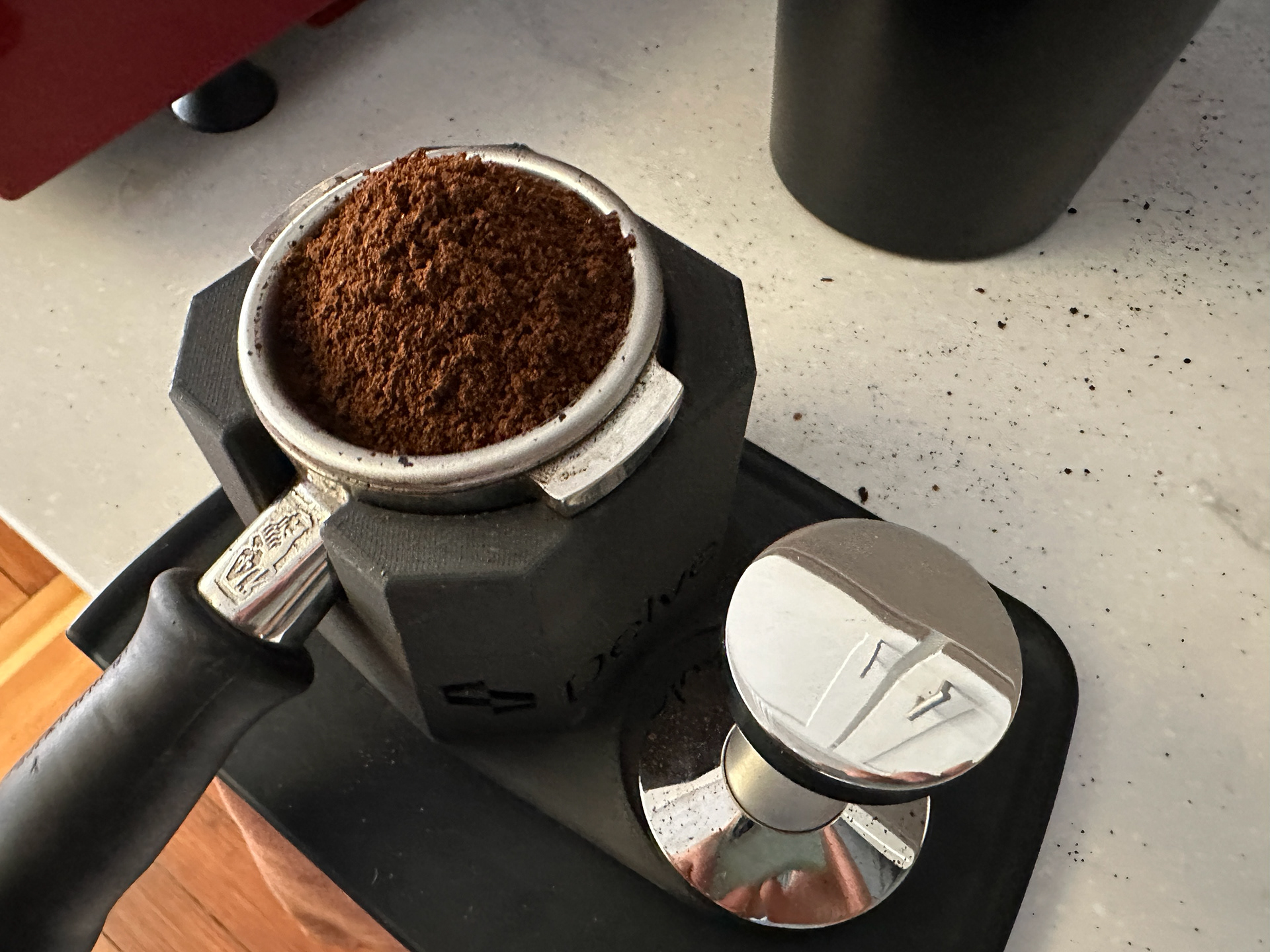
Portafilter at tamping station
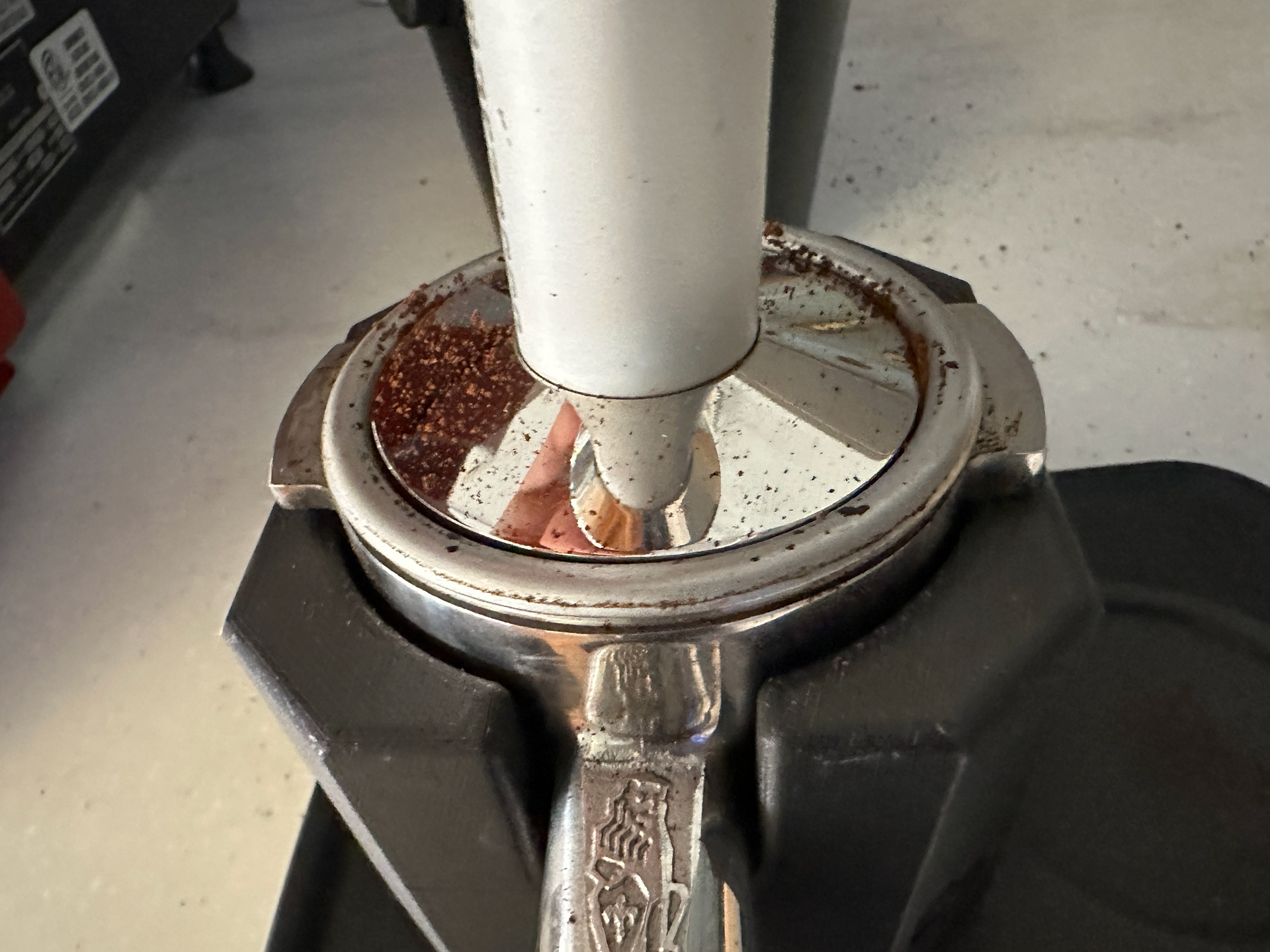
Grounds can often escape around the edge of the tamper, especially when the pile of grounds can't be tapped and leveled before being tamped
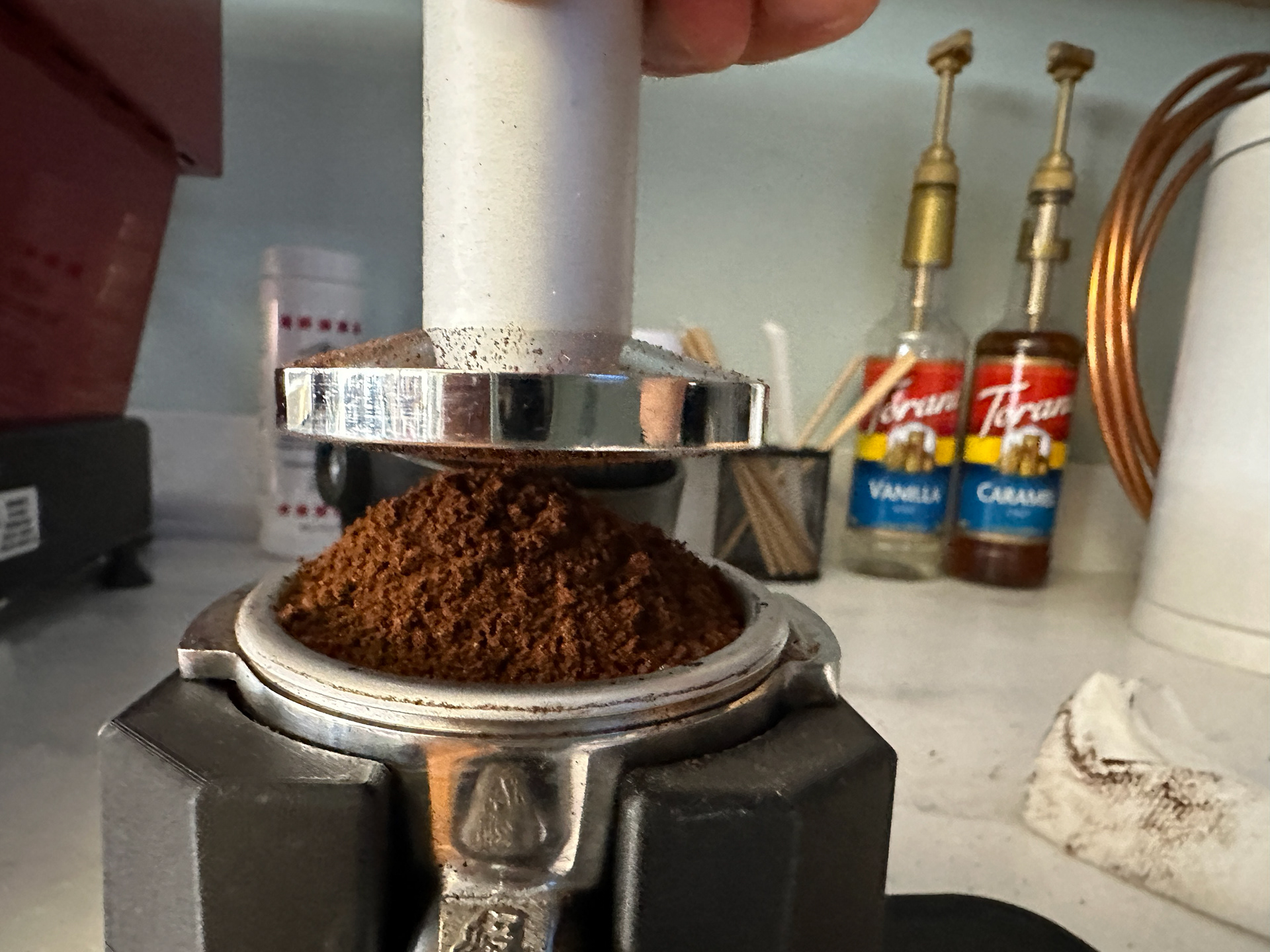
Attempting to tamp a pile of grounds? Maybe we should tap and level it first. But tapping to level it will often spill grounds too!
Concept Pitch
View the pitch deck below!
Nothing was analyzed or engineered yet, but we go over the problem statement and outlined our expectations of components/subassemblies.
Early Pitch Concept Model
A short video showing the initial 3d printed model used to pitch the project and demonstrate its most basic capabilities. It's sized to be absolutely adorable in order to reduce the print time.
Superglue was used extensively to hold everything together.
Final Presentation
Final presentation with all calculations included
Modeling done in Onshape, renderings in Keyshot
Final Design Render Gallery
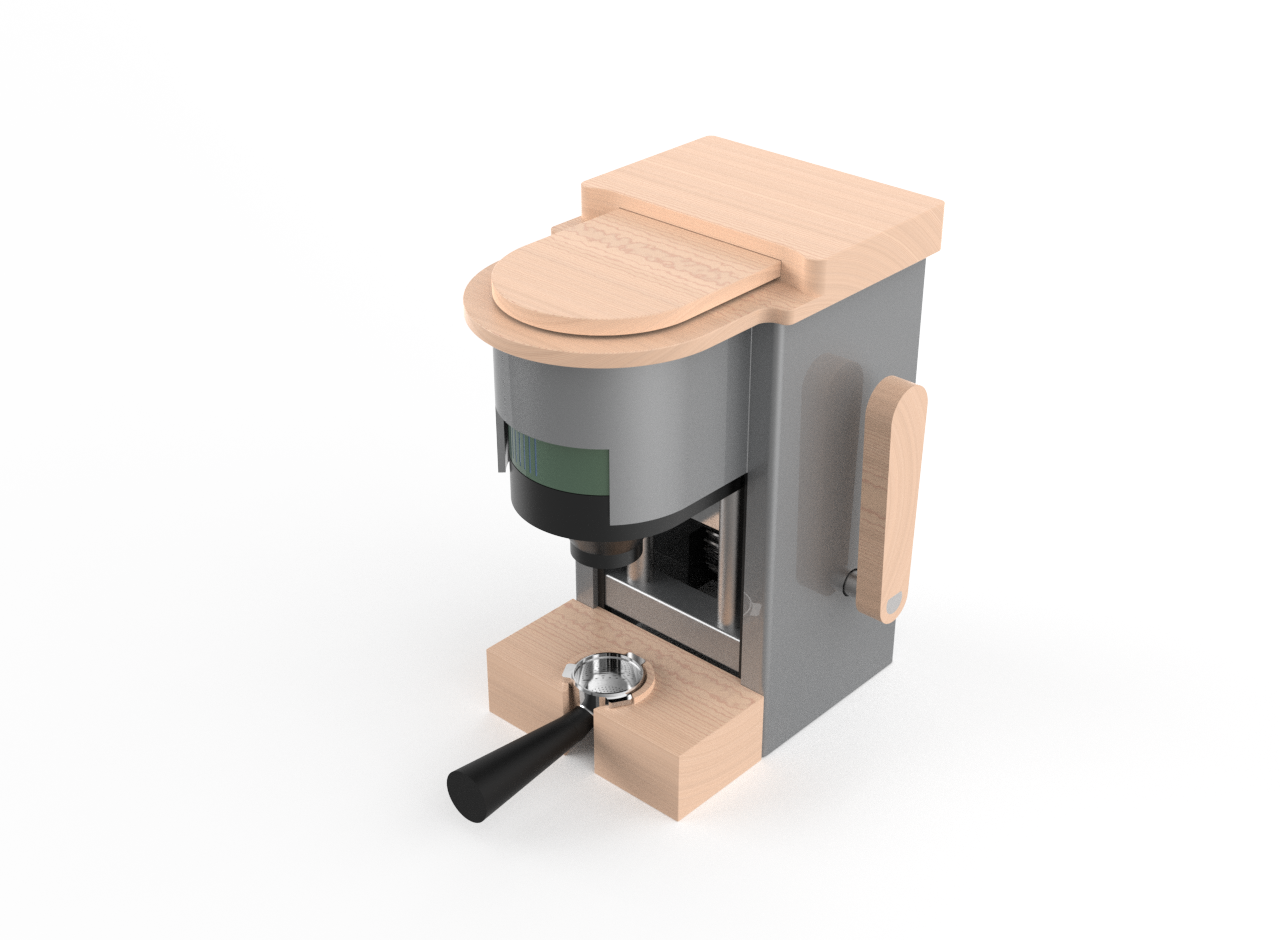
Top down view
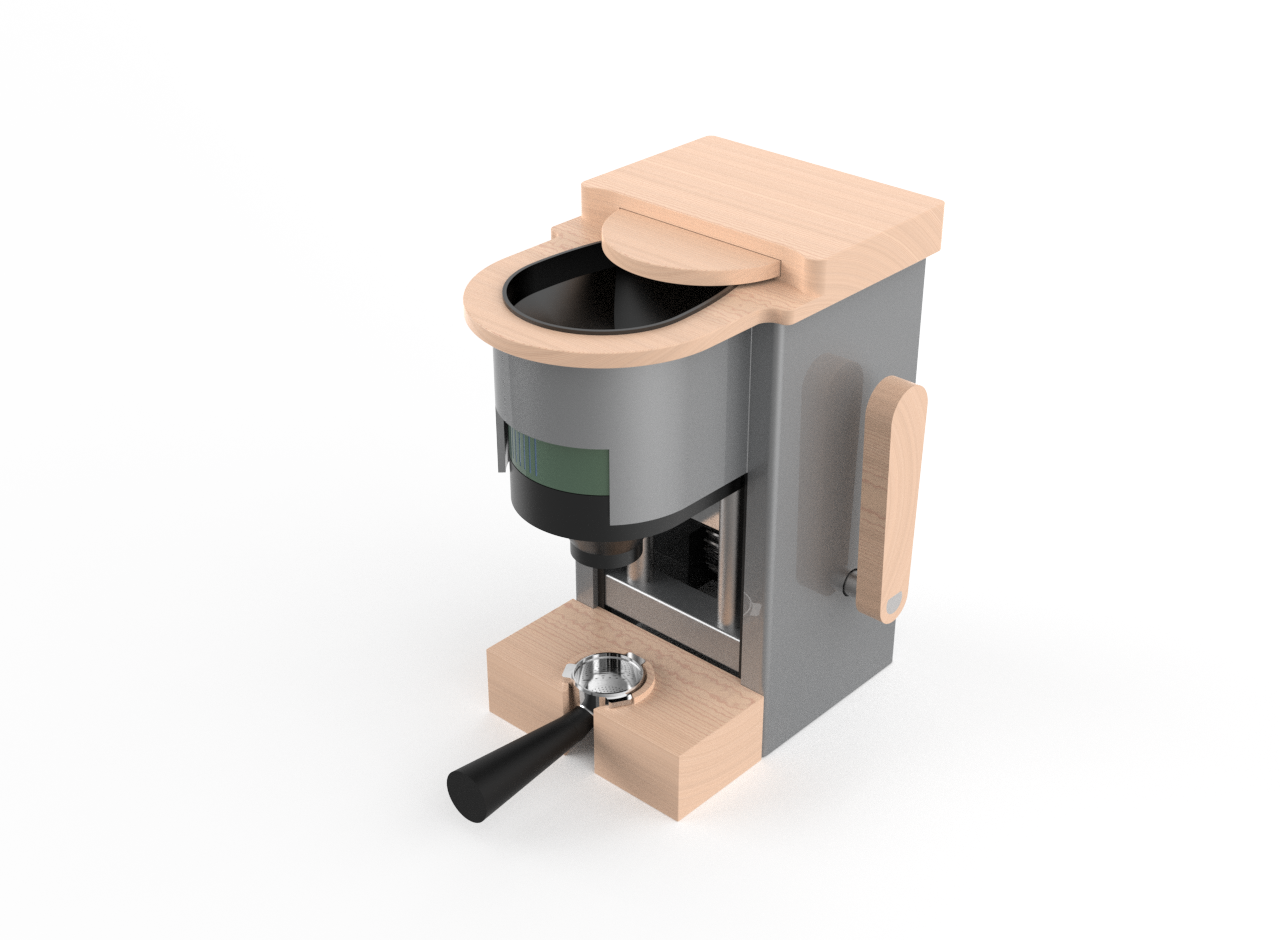
Access hatch slides back to expose the hopper
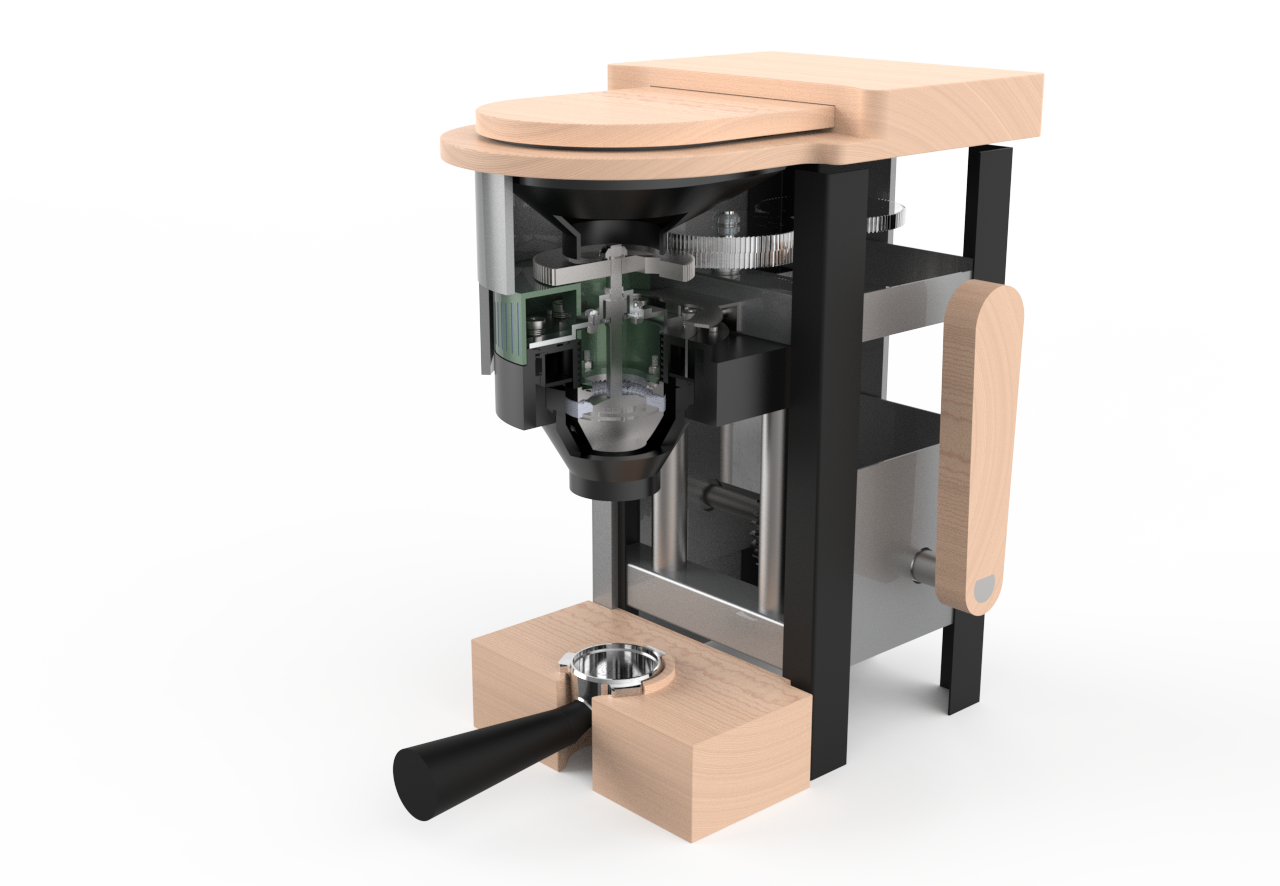
Cutaway view showing the internals
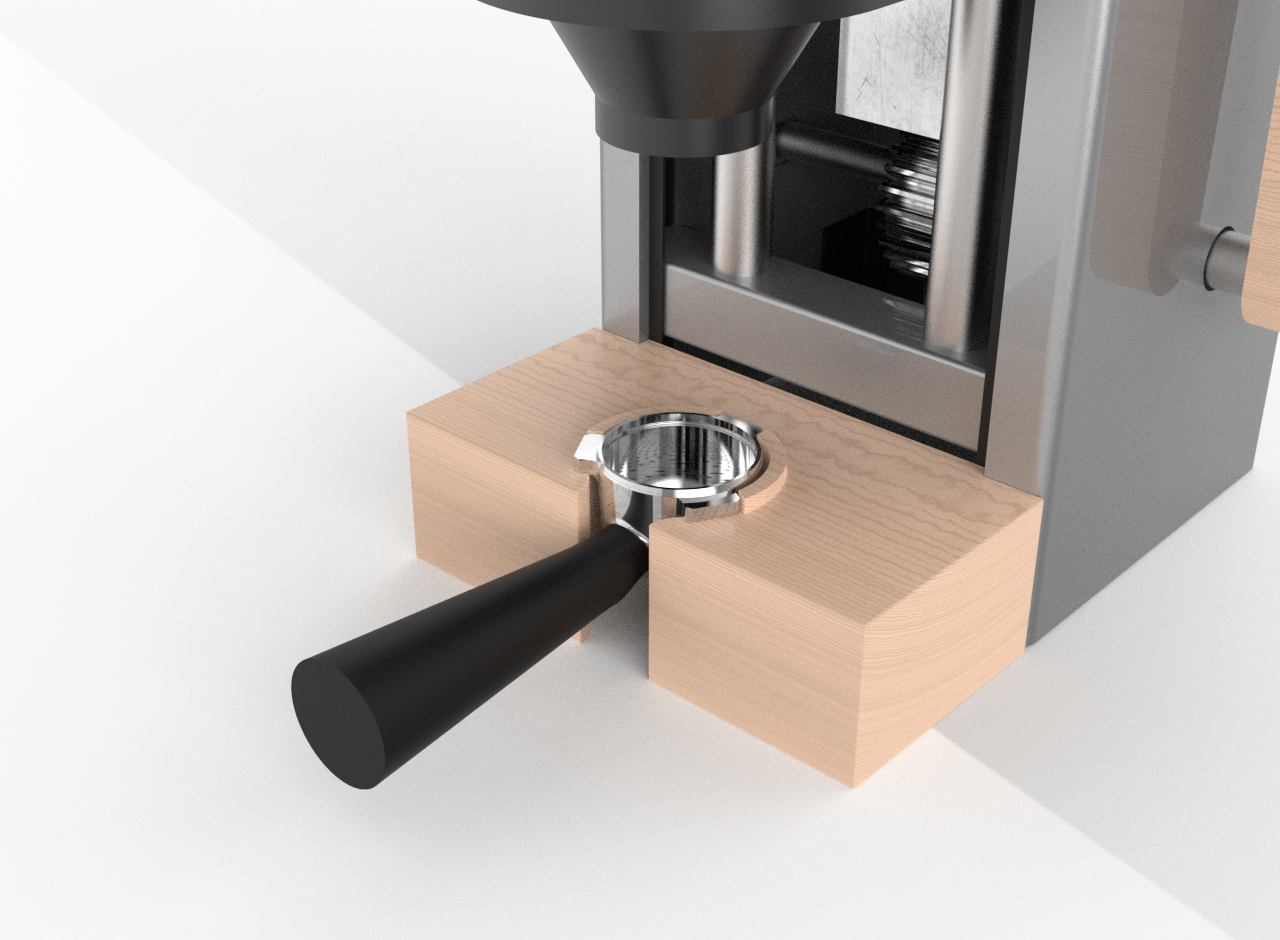
Portafilter holding block
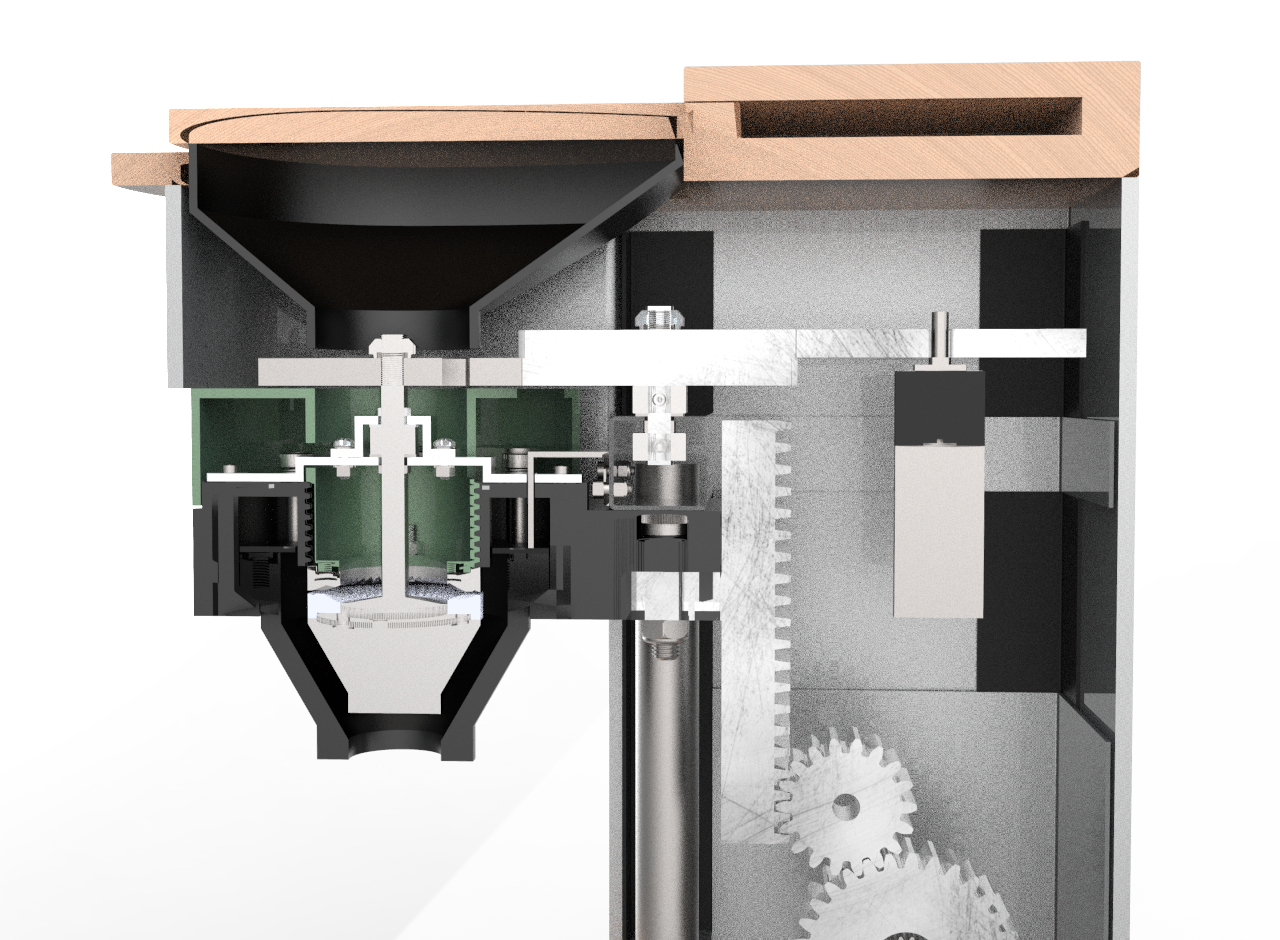
Cutaway side view of all mechanisms
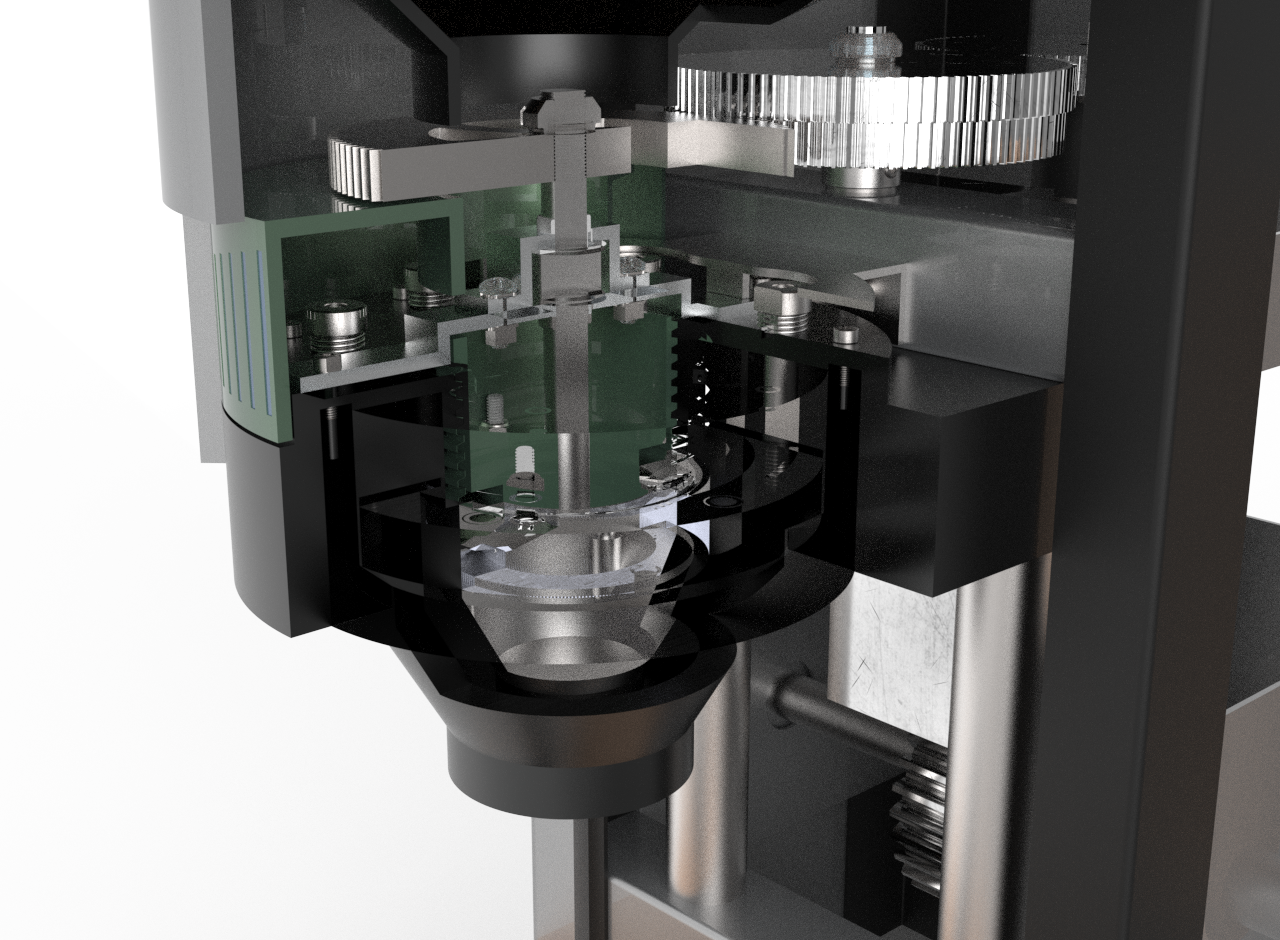
Cutaway view of the main mechanisms. The burr grinder and tamper subassembly
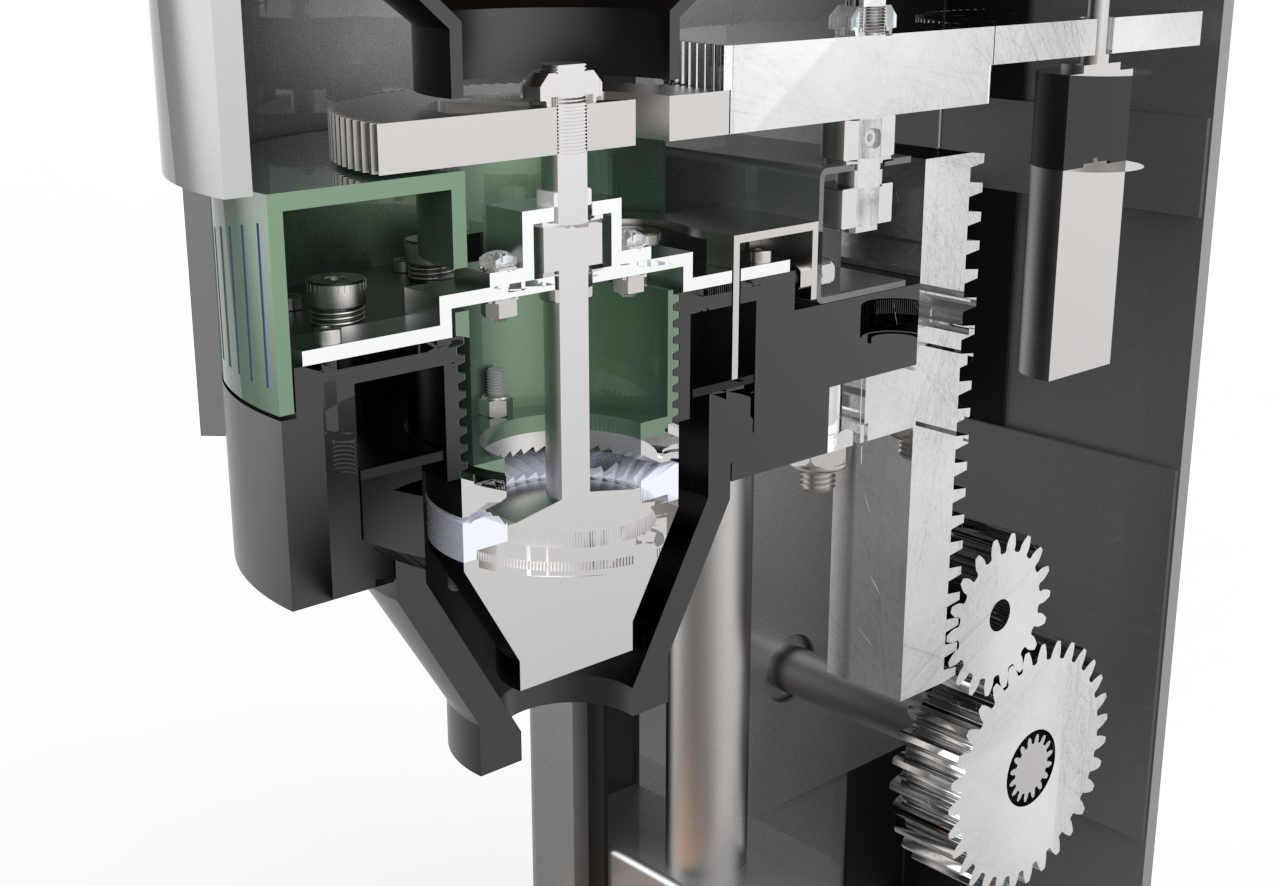
The green dial can be used to adjust the grind size by lifting and lowering the top burr
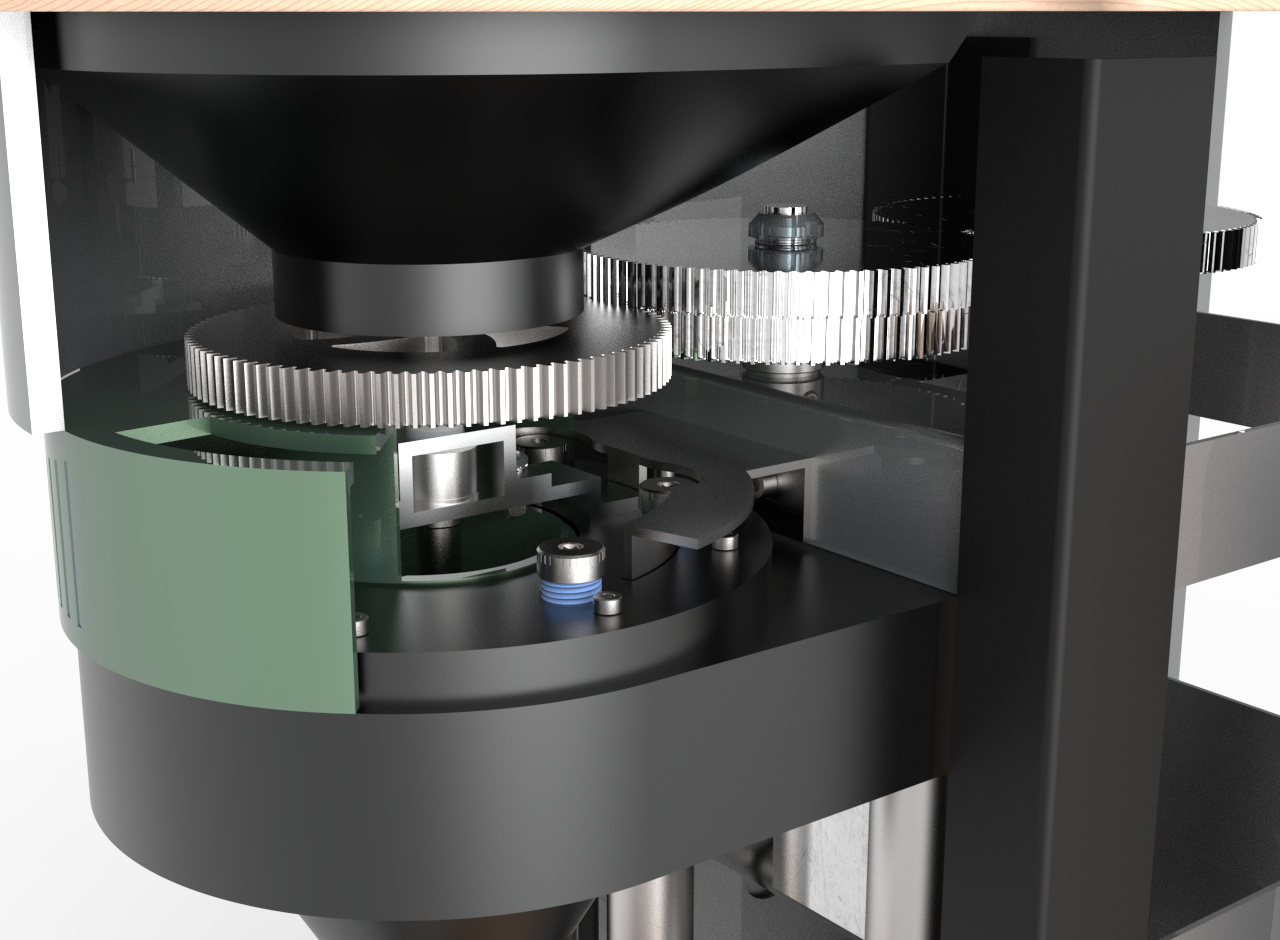